As a new DIY tuner you're faced with a whole bunch of new terminology to get to grips with, mostly to do with the construction of the ski or board. This section is designed to give a brief explanation of the parts of the ski/board that you'll be working on when tuning.
Fig 1 shows a section of a ski, although boards are very similar. The ski body is usually made up of a number layers of wood, plastic, metal, carbon fibre & foam. Alternatively it could be a type of box construction known as a torsion box. However it's constructed the ski body is commonly known as the ‘core' - hence the term ‘core shot' when rock damage penetrates the base of the ski & into the body of the ski. The top layer that covers the ski & on which the graphic design is printed is called the top sheet & the portion of the top sheet that goes down either side of the ski to meet the metal edges is known as the ‘sidewall'.
This leaves the other two components which are of primary interest to us tuners, namely the base & the edges:
Most bases are constructed from HDPE (high density polyethylene) which is known as P-Tex, although this is actually a trade name. They can also be made from UHMW-PE (ultra high molecular weight PE) with DuraSurf being a manufacturer of such bases. Both are available in Extruded or Sintered form.
Extruded is cheaper, found in entry and mid level equipment. 3 grades of extruded: 1000, 1500 and 2000. The higher the grade, the greater the resistance to wear and the tougher the base material is. Extruded bases do not hold wax as well which means it is more important to regularly wax these bases to avoid drying out.
A sintered base is superior - it's more durable, faster and holds wax better than an extruded base. It's also more expensive and difficult to repair. It comes in three general grades: 2000, 4000, 8000. This type of base is found on higher performance equipment. To further improve performance manufacturers will add ceramic fibres to improve wear resistance. Graphite is also added to reduce static build up at higher speeds to aid performance and turning.
Structure is the name given to the fine longitudinal grooves in the base of the ski that breaks the surface tension of the film of water between the ski base & the snow. Without the structure's action the ski would 'stick' to the snow. Not only do the grooves break the surface tension but they also act like the tread on a car tyre to remove/shed the water away efficiently. For a high-end ski racer the pattern & depth of the structure has to be chosen to match the conditions & is as important to their performance as tyre choice is to a racing car.
The majority of edge material on the market today are steel with has a Rockwell hardness of 48. Some companies claim differently but it's pretty much the same for all edge material.
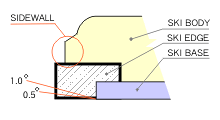
Fig 1 - Base edge angle
Fig 1 also shows were the base edge angle is cut (usually 0.5, 0.7 or 1 degree) which is measured from the horizontal. The amount base edge angle determines how much the ski needs to be tipped until the side edge engages in the snow - so 1 degree base angle needs the ski tipping twice as much as a 0.5 degree base angle.
As can be seen from the diagram once the base edge has been cut (to say 1 degree) it cannot be reduced as metal cannot be added. The only way to reduce the base edge angle is to grind material off the base & the edge until the base edge angle is back to zero, & then re-cut it.
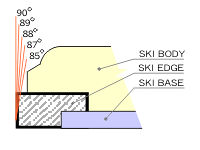
Fig 2 - Side edge angle
Fig 2 shows the side edge angle. This diagram is of the US style of nomenclure were the angle is measured from the horizontal (ie, 90, 89, 88 or 87 degrees etc), however in Europe we measure the side edge angle from the vertical, so 89 degrees = 1 degree, 88 = 2 degrees & 87 degrees = 3 degrees etc.
The more acute the side edge angle is cut the greater the amount of bite the edge has once it's been engaged in the snow by tipping the ski over & across the base edge.
What can also be seen in Fig 2 is how the sidewall could interfere with cutting a clean side edge angle as continuous tuning will reduce the clearance until the sidewall snags on the file/diamond files etc. This is when the sidewall needs to be stripped/cut back. It's also quite common for new skis to need their sidewall's removing before the side edge can be polished.
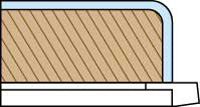
Fig 3 - 1 degree base edge & 1 degree side edge
Fig 3 shows a 1 degree base angle & a 1 degree side angle. The actual angle at the junction of the two edges is a right-angle. A 1 degree side angle is the minimum angle required to obtain any kind of decent edge hold on firm snow. An example of a ski that's made with this edge specification is the Rossignol B2.
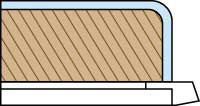
Fig 4 - 1 degree base edge & 3 degree side edge
Fig 4 show a 1 degree base edge & a more acute 3 degree side edge angle. When specifying edge angles the base edge is always quoted first, then the side - so this set-up would be a 1,3.
The greater the side angle the more the edge will bite in hard snow to give better edge grip, however if the edge angle is extreme then it will become duller quicker & require more frequent maintenance. In my opinion a 3 degree side edge angle gives the best edge grip with no loss of durability. Interestingly Atomic ship all their skis with a 1,3 set-up, including all their powder models.
When tuning edges, & assuming that you want to stay with the manufacturer's specified angles, it's therefore important to know what those angles are so that you can use the correct angle guides etc. I have compiled a list of the manufacturer's specifications which can be found in the ‘Manufacturer's Data' section.